SlagCEM
SlagCEM - Portland cement and pig iron from steel mill slag
Resource-efficient circular economy - construction and mineral material cycles (ReMin)
The SlagCEM project is researching and optimizing the production of main cement constituents from steelworks slag (SWS) with simultaneous recovery of pig iron. The process used in the project not only enables the recovery of bound iron, but also produces a material similar to Portland cement, which can be used as a high-quality binder.
The project is being funded as part of the "Resource-efficient circular economy - construction and mineral material cycles (ReMin)" funding measure. "ReMin" is part of the BMBF research concept "Resource-efficient circular economy" and is aimed at resource-efficient construction and the expanded use of mineral secondary raw materials from construction waste, slag, ash and mining residues.
Steel mill slag - a by-product with potential
Every form of steel production produces slag - so-called steelworks slag (SWS). While granulated blast furnace slag from pig iron production, known as granulated blast furnace slag, has long been used in the cement industry, there are currently no comparable high-quality uses for steelworks slag. They are mostly used in transportation construction. Bound iron (up to 30 wt.-%) is thus lost.
Steelworks slag, such as Linz-Donawitz (LD) slag, offers a significantly higher utilization potential due to its composition. In addition to high concentrations of CaO (calcium oxide) and SiO2 (silicon dioxide), they contain up to 30 wt.-% Fe2O3 (iron(II,III) oxide). This makes the recovery of iron for recycling into steel production an attractive option. By separating the iron, the chemical composition of the slag is brought very close to that of Portland cement clinker and, among other things, cement clinker phase alite is formed - the most important strength-forming component of Portland cement. This allows pig iron for the steel industry to be recovered from LD slag and a hydraulic binder to be produced.
Large-scale implementation of the high-temperature process
In order to recover the largely oxidic iron, it must be reduced to metal in a high-temperature process. In preliminary investigations, steelworks slag was melted in a small-scale electric arc furnace at temperatures of around 1800 degrees Celcius and the iron oxide contained was reduced to metallic iron. In a large-scale process, however, such high temperatures are uneconomical and problematic with regard to the refractory material. The reduction should therefore take place on liquid SWS directly after tapping in the steelworks at around 1600 degrees Celcius.
SlagCEM is pursuing the goal of adapting the process in such a way that it can be implemented on an industrial scale under economic conditions. To this end, the chemical composition is modified so that the melting temperature of the slag and its viscosity are within a technically suitable range and a product with good cementitious properties is created.
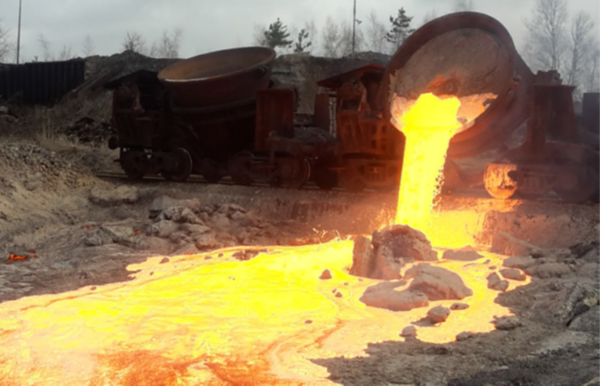
Project team from research, steel and cement industry
Expertise from research, the steel and cement industries is required to develop a technically, logistically and economically manageable process and to ensure that both the recovered pig iron and the binder produced are marketable. The project partners are cooperating closely with the cement manufacturers CEMEX Deutschland AG and Spenner GmbH & Co. The Institute for Building Materials Research e. V., the German Aerospace Center (DLR), the Technical University of Berlin and the Federal Institute for Materials Research and Testing (BAM) are investigating the effects of modifying ArcelorMittal's LD slags on their melting behavior and the cementitious properties of the product. The online LIBS (Laser Induced Breakdown Spectroscopy) process from LTB Lasertechnik Berlin enables the material changes to be observed during the experiments. One aim of the project is to plan the large-scale implementation of the process at the Eisenhüttenstadt steelworks site.
Following the evaluation of the grindability of the product produced by thyssenkrupp Industrial Solutions, its performance as a binding agent will be evaluated on a technical scale by the cooperation partners CEMEX and Spenner. A market analysis by the companies involved enables the market value of the products produced to be assessed. The life cycle assessment (LCA) of the entire recycling process, prepared by the Öko-Institut, allows a final assessment of the environmental impact of the process.
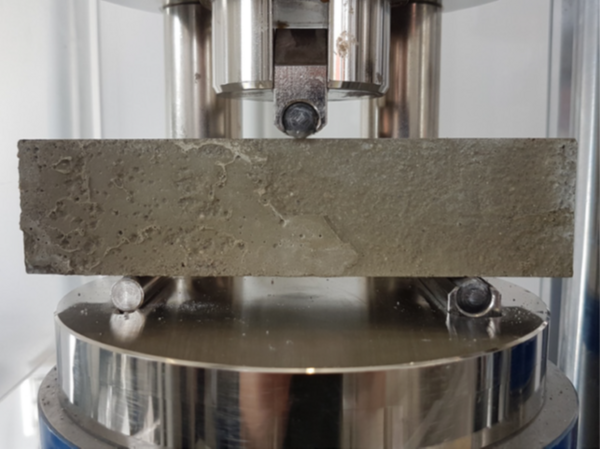
Funding measure
Resource-efficient circular economy - construction and mineral material cycles (ReMin)
Project title
SlagCEM - High-quality cements and pig iron from steel mill slag
Duration
01.02.2021-31.01.2024
Funding reference
033R254
Funding volume of the consortium
1,855,651 euros
Contact
Dr. Christian Adam Federal
Institute for Materials Research and Testing (BAM)
Unter den Eichen 87 | 12205 Berlin
Phone: 030 8104-5670
Email: christian.adam@bam.de
Project participants
ArcelorMittal Eisenhüttenstadt; Technische Universität Berlin; Deutsches Zentrum für Luft- und Raumfahrt e. V. (DLR); FEhS - Institut für Baustoff-Forschung e. V.; thyssenkrupp Industrial Solutions; Öko-Institut e. V.; LTB Lasertechnik Berlin
Data sheet
Download data sheet